Okay, so today was a big day – finally getting to work on the chemical processes in the new factory, section 1.15. It’s been a long time coming, and honestly, I was a little nervous.
First thing I did was double-check all the safety protocols. I mean, working with chemicals is no joke, you gotta respect the materials. I went through the checklists, made sure all the emergency equipment was in place, and that everyone on the team knew the procedures. Better safe than sorry, right?
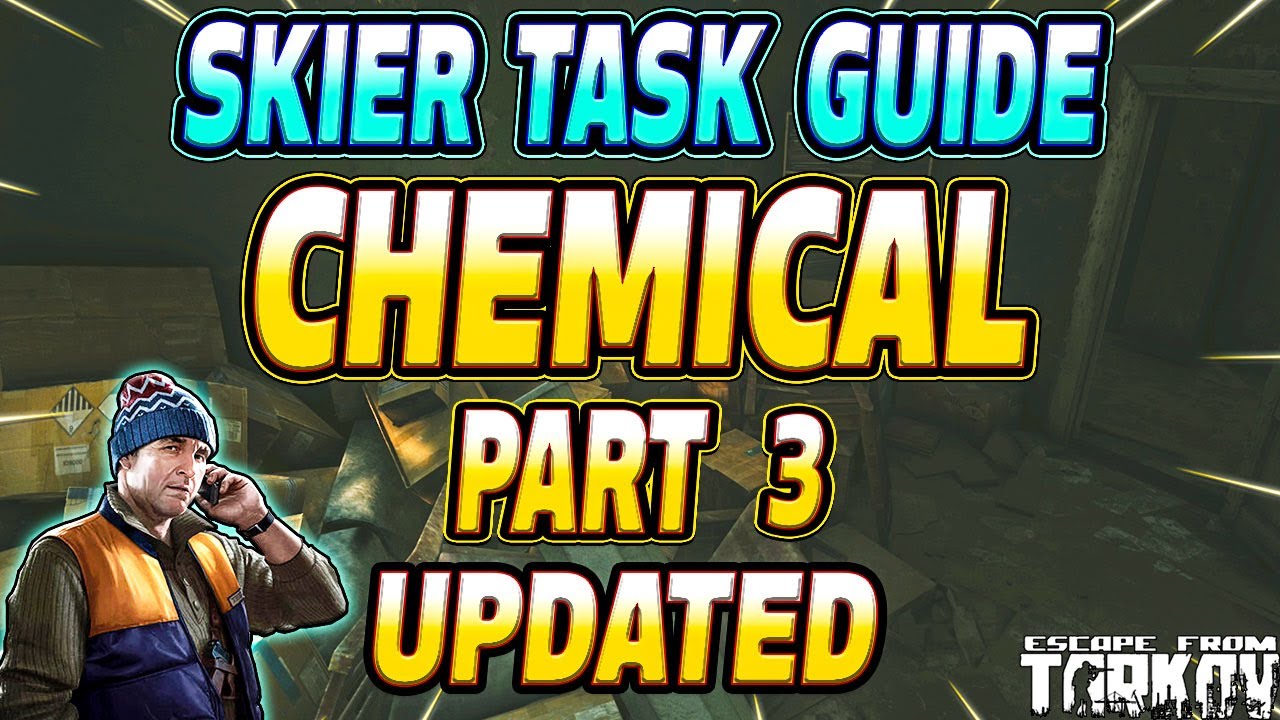
Getting Started
Next up, I gathered all the materials we needed. We’re starting with a relatively simple reaction, nothing too crazy, just to get a feel for the new equipment and the layout of this section. I laid everything out, making sure it was all organized and easy to access. It’s amazing how much smoother things go when you’re not scrambling for stuff.
- Checked reagent purity.
- Calibrated the scales – super important for accurate measurements.
- Inspected all the glassware for any cracks or imperfections.
Running a test
Then, it was time to actually start the reaction. I carefully measured out the reactants, following the standard operating procedure (SOP) to the letter. Added them to the reactor, made sure the stirring was at the right speed, and set the temperature controller. This part always feels a little like magic, watching the chemicals combine and transform.
I kept a close eye on everything – temperature, pressure, the color of the mixture. Documenting every step is crucial. I used my trusty notebook (yeah, I’m old school like that) and jotted down all the readings, any observations, and the exact times of each step. If something goes wrong, you need that detailed record to figure out what happened.
Troubleshooting and adjustments
Of course, not everything went perfectly smooth. We had a slight issue with the temperature fluctuating a bit more than I’d like. So, I troubleshot the problem, checked the connections, and made a small adjustment to the cooling system. Took a few minutes, but we got it stabilized. It’s all part of the process, learning the quirks of the new equipment.
The outcome
Finally, after letting the reaction run for the specified time, we stopped it and started the analysis. We took samples, ran some basic tests to check the purity and yield of the product. The initial results looked promising! Not perfect, but definitely within the acceptable range for a first run in a new setup. I was feeling pretty good.
So, that was my day – a successful start to the chemical processes in the new factory. Lots more to do, but it’s always satisfying to get that first one under your belt. I’ll keep you all posted on how things progress!
