Okay, folks, let’s dive into my recent adventure with “logistics planning mid level.” I gotta say, it was a bit of a learning curve, but I managed to pull through, and I’m here to share the messy, real process.
First things first, I started by grabbing all the data I could find. We’re talking sales forecasts, inventory levels, transportation schedules – the whole shebang. It was like drinking from a firehose, honestly. I just dumped it all into a giant spreadsheet. My eyes almost crossed, but hey, gotta start somewhere, right?
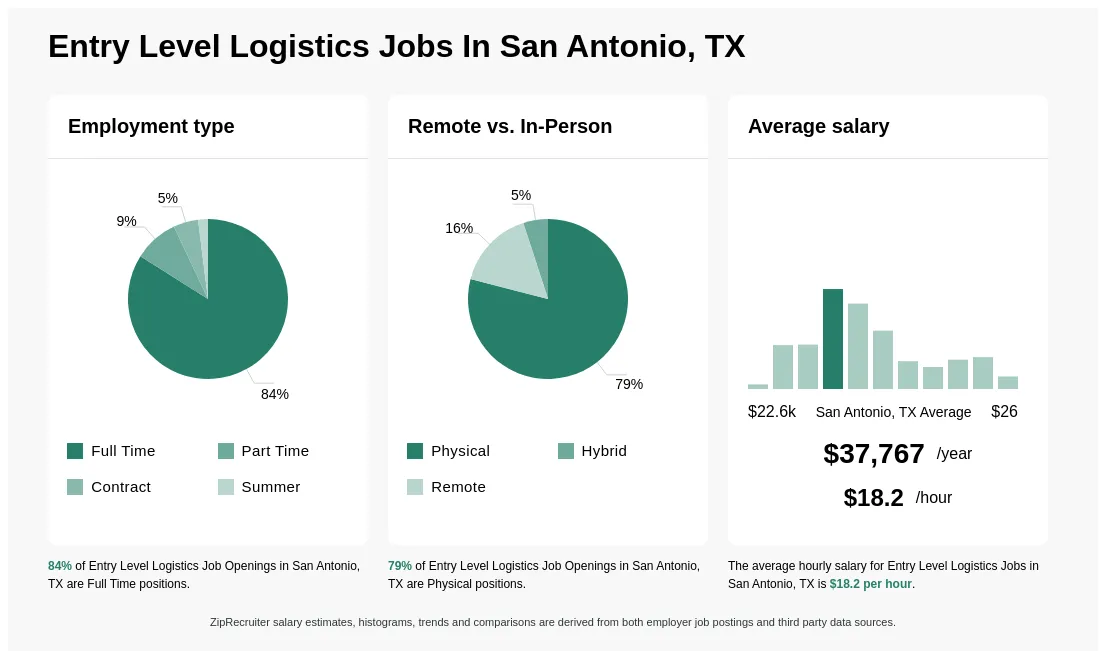
Getting Organized (or Trying To)
Next, I tried to make some sense of this data monster. I categorized everything – you know, separating apples from oranges. I grouped products by type, locations by region, and transportation methods by… well, method. It was slow going, and I definitely made a few wrong turns, but eventually, things started to look a little less chaotic.
- Sales data – breaking it down by product and time period.
- Inventory – figuring out what we had, where it was, and how much it cost to store.
- Transport – checking out truck schedules, shipping routes, and those pesky fuel prices.
Finding the Bottlenecks
Once I had a (somewhat) organized spreadsheet, I started looking for trouble spots. Where were things slowing down? Where were we spending too much money? I used some simple formulas to calculate things like lead times, transportation costs per unit, and inventory turnover rates. Nothing fancy, just basic math to point me in the right direction.
I noticed that that one of our main product have a problem that the delivery times were all over the place, causing stockouts and angry customers. So, I focus on this.
Making a Plan (and Adjusting It… A Lot)
This is where the “planning” part really kicked in. Based on what I saw, I started sketching out some possible solutions. Maybe we needed to renegotiate with our trucking company, maybe we need some changes. I played around with different scenarios, changing the numbers in my spreadsheet to see what would happen. “What if we shipped more frequently?” “What if we used a different warehouse?” It was a lot of trial and error, I am not use any fancy software or tools.
Then I chose to added another supplier to provide the shortage parts, and it took me a lot of time to conpare different supplier and negotiate with them.
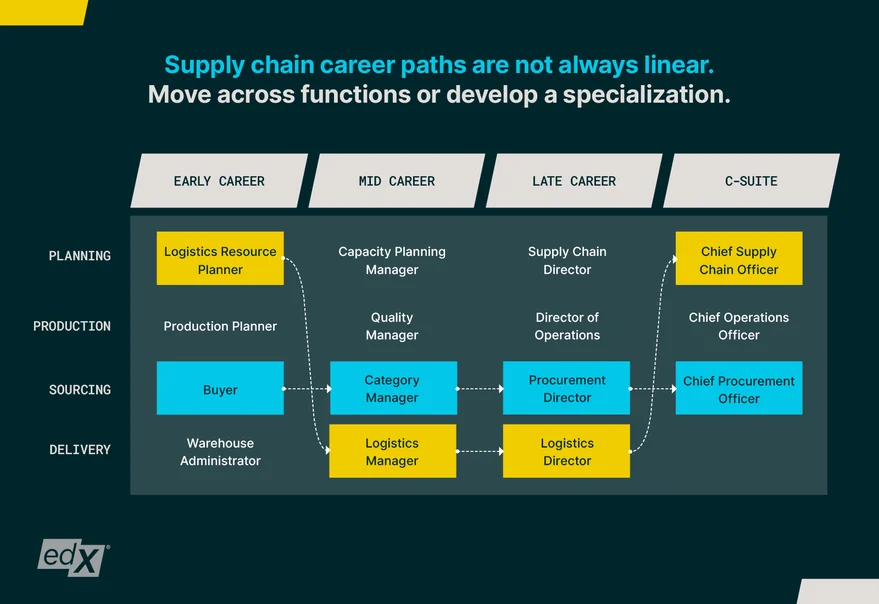
The Results (Fingers Crossed!)
Finally, I put my revised plan into action. I communicated the changes to everyone involved – warehouse staff, truck drivers, sales team – and crossed my fingers. Of course, it wasn’t perfect. There were a few hiccups along the way, but overall, things improved. We saw fewer stockouts, delivery times got more consistent, and we even managed to save a little bit of money on transportation costs. I am very happy I made it!
So, that’s my “logistics planning mid level” journey in a nutshell. It wasn’t glamorous, and it definitely wasn’t easy, but I learned a ton, and I’m excited to tackle the next challenge. Remember, it’s all about digging in, figuring things out, and not being afraid to make mistakes. You got this!